The Evolutionary Leap of Welding Robots: Transforming the Manufacturing Landscape
Writer:admin Time:2025-03-03 14:36 Browse:℃
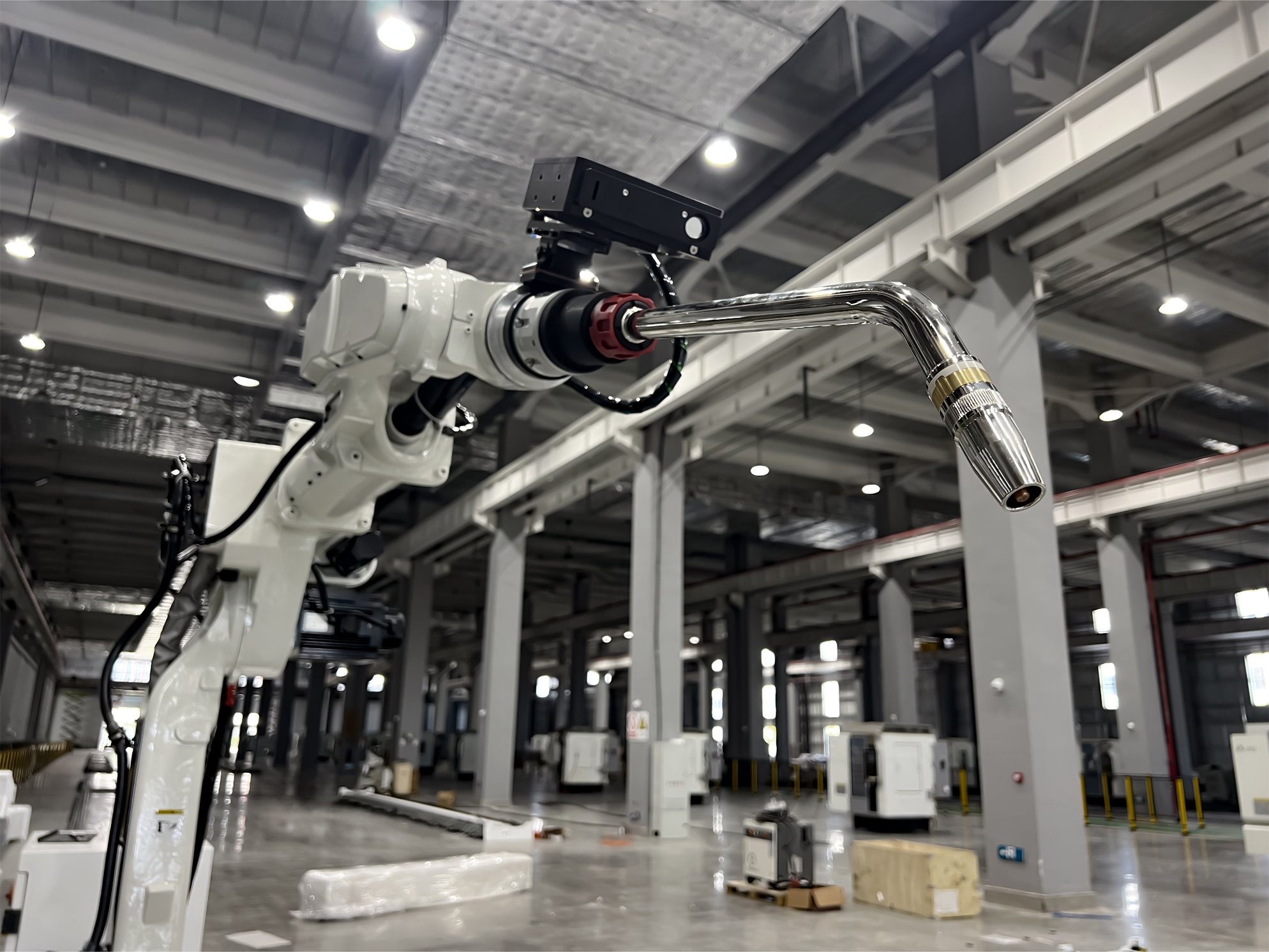
Welding Robots: The Evolution, Benefits, and Future of Automated WeldingWelding is hard. Finding skilled welders? Even harder. Keeping them safe and ensuring consistent quality? A constant challenge. What if robots could swoop in to handle these issues? Welding robots are becoming more common and changing how things are made.
A Brief History of Welding Robot Development
Welding robots weren't built overnight. It took time, innovation, and lots of trial and error. So, let's explore how these metallic marvels came to be. The journey started long ago, way before computers got smart.
Early Automation in Welding
People first tried to make welding easier way back in the 1960s. They came up with basic machines that could do simple welds. Think of it as the first step toward modern welding automation. These early setups weren't robots. They were more like automated tools. However, they proved that machines could help with welding tasks.
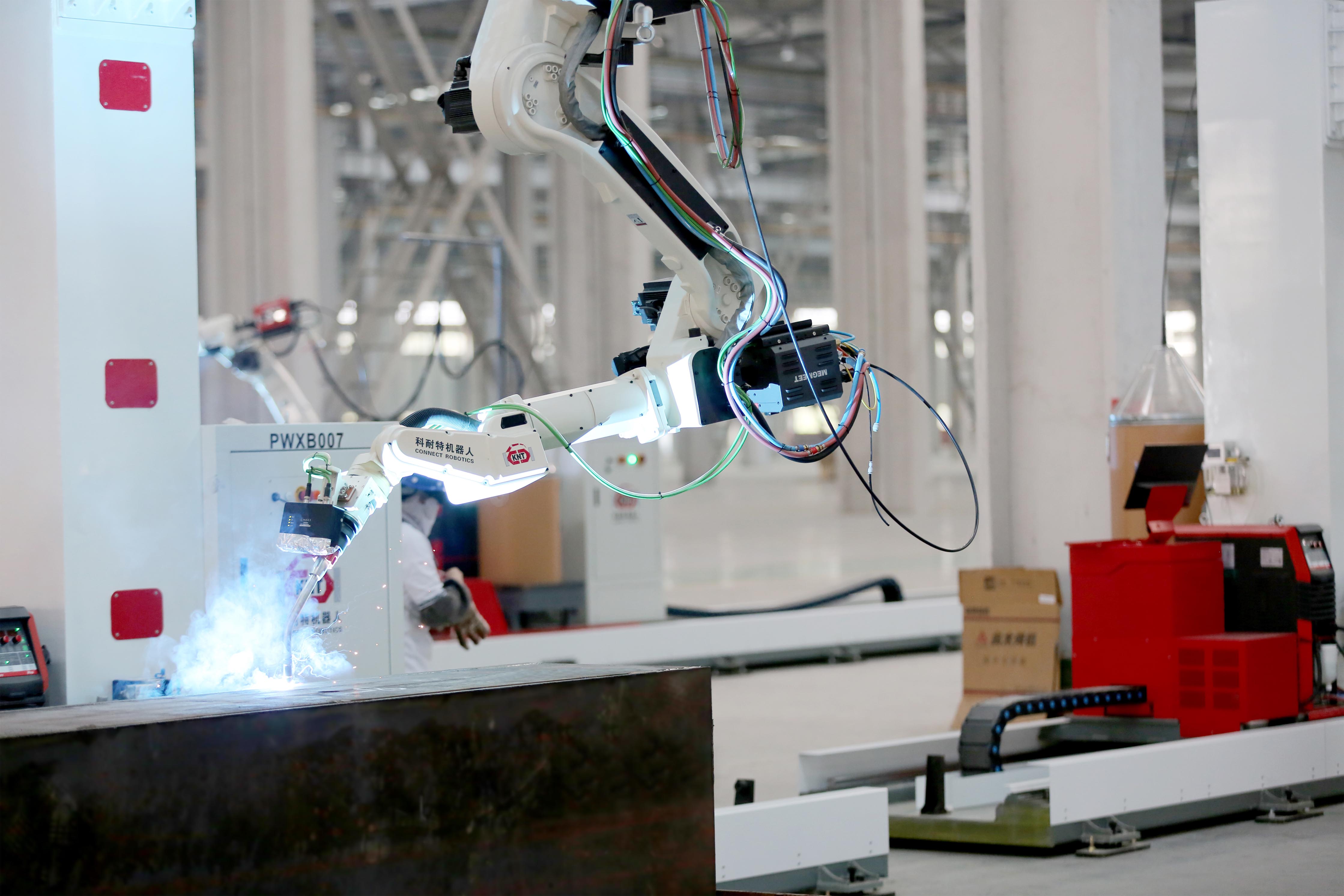
Key Milestones in Welding Robot Technology
The 1980s saw big changes. Robots became more advanced. They could now be programmed to perform more complex welding jobs. Better control systems helped robots move precisely. Improved welding methods meant robots could handle different materials. These advances turned robots into valuable tools for manufacturers.
The Rise of Industrial Robotics and Welding
As industrial robots spread, welding robots got better. The auto industry jumped on board. They used robots to weld car parts quickly. This pushed robot makers to create even more effective systems. Soon, welding robots were used everywhere. This growth spurred more innovation and competition, resulting in today's advanced welding robots.
Advantages of Using Welding Robots
Welding robots provide clear advantages. They boost production and improve quality. Worker safety gets a huge lift. Let's break down these perks.
Increased Productivity and Efficiency
Robots weld faster than humans. They don't need breaks or get tired. A robot can keep welding all day, every day. Cycle times go down and more parts get finished. Companies see big gains in efficiency and output.
Enhanced Weld Quality and Consistency
Robots make the same weld over and over. This removes human error. Welds are stronger and more accurate. Fewer defects mean less waste. Businesses enjoy better product quality.
Improved Worker Safety and Reduced Risk
Welding can be dangerous. Fumes, sparks, and heat pose risks. Robots take on these hazards. They keep workers away from harm. Injuries go down, and the workplace becomes safer.
Types of Welding Robots
Not all welding robots are equal. Different jobs require different tools. Here are some common types.
Articulated Welding Robots
These robots have arms that can bend and twist. This gives them great reach. They can weld in tight spots. Auto plants often use them for their flexibility. They can handle complicated welding tasks.
SCARA Welding Robots
SCARA robots are fast and precise. They work best on flat surfaces. They excel at quick, repeated actions. Electronics firms use them for small part welding. SCARA robots bring speed and accuracy to specific jobs.
Collaborative Welding Robots (Cobots)
Cobots are designed to work with people. They have sensors that stop them from causing harm. They can help welders with tricky tasks. Cobots make welding more approachable and safer.
Applications of Welding Robots Across Industries
Welding robots are useful across many fields. They are transforming the way things are made. Check out some key examples.
Automotive Manufacturing
The auto industry relies heavily on welding robots. They weld car frames, bodies, and parts. Robots ensure consistent welds on every vehicle. This leads to better quality and safer cars.
Aerospace and Defense
Aerospace needs precise welds. Welding robots meet those strict needs. They weld plane parts, missile components, and satellites. High accuracy and reliability are vital in this field.
Construction and Infrastructure
Bridges, pipelines, and buildings all require welding. Welding robots are stepping up to these big projects. They weld steel beams and pipes safely and efficiently. This helps build stronger infrastructure.
The Future of Welding Robots
The future looks bright for welding robots. New tech is making them even smarter. AI, advanced sensors, and cobots are set to play big roles. These developments will change welding for good.
Integration of Artificial Intelligence and Machine Learning
AI is making robots more intelligent. They can now learn from experience. Machine learning helps them optimize welding paths. Robots can adjust to changes automatically. This leads to better welds and fewer errors.
Advances in Welding Sensors and Control Systems
Better sensors provide real-time feedback. Robots can now monitor weld quality as they work. They adjust settings to maintain perfect welds. These advances ensure top-notch results.
The Growing Role of Collaborative Robots in Welding
Cobots are becoming more common. They work safely alongside people. Cobots assist with complex or delicate tasks. This collaboration improves both efficiency and worker satisfaction.
Conclusion
Welding robots offer many benefits. They boost productivity, improve quality, and enhance safety. The rise of AI and cobots promises an even brighter future. Automation is becoming more vital in the welding industry. Welding robots will continue to shape how things are made.